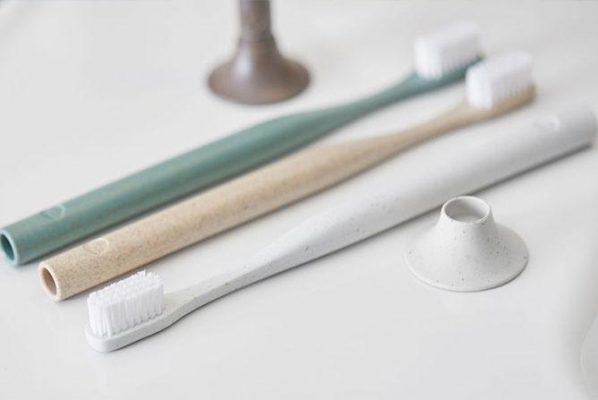
Feb. 24 (UPI) — From toothbrushes in luxury island resorts to 3D printing filament, products made from hemp-based plastics are popping up in consumer products since the crop was made legal in the United States in 2018 for the first time in 80 years.
They are the latest generation of c which are plastic materials produced from renewable sources such as agricultural by-products, straw, wood chips, sawdust and recycled food waste — and now hemp.
Hemp seems to satisfy some plant-based plastics researchers looking for alternatives to plastic waste that has filled landfills and oceans.
Hemp fiber, for example, is used in one of the plant-based plastics developed by Chad Ulven, an associate professor of mechanical engineering from North Dakota State University, through his Fargo-based company, c2Renew.
“There’s a craze around being able to grow hemp finally in the United States and 3D print and play with the material,” Ulven said.
His work furthers research with polylactic acid, a resin created from corn byproducts. It is formulated with organic fillers such as coffee and beer waste, flax, cotton, seed hulls and even charred industrial carbon.
Hemp-based plastics now are expanding to both injection-mold and 3D additive manufacturing, Ulven said.
Hemp-based filament, melted and layered by a 3D printer, creates a caramel-colored plastic surface flecked with organic specks, said John Schneider, CEO of 3D-Fuel, a printer filament company based in Fargo and Ireland. Customers use it to print custom decor items like lampshades and vases.
Specialty parts
“We see a lot of people who use it for specialty parts, especially in the cannabis industry,” Schneider said. These include frames for promotional sunglasses, as well as retail fixtures, such as hinges and product sales stands.
It took a while for Denver-based Sana Packaging’s chief executive, Ron Basak-Smith, to locate a source for hemp-based biocomposites, or plastics with hemp fillers, to make sustainable packaging for cannabis.
Now Sana uses hemp plastic and recycled ocean plastic, made with injection molds. The company sells to 200 cannabis companies, Basak-Smith said.
“Because of the ability to [easily] produce plastics, we got ourselves into single-use disposable culture, and that has caused a dysfunctional system,” he said.
The infrastructure to produce petroleum plastics grew up as a way to use byproducts of the oil industry and has led to a culture of single-use disposable products. That can’t be changed overnight, c2Renew’s Ulven said.
“That industry has been so huge and such an impact on our daily lives. I tell my students to try and get through a single day without using plastic. It’s impossible,” he said.
Ulven works with a landfill that burns carbon waste, capturing toxic fumes for repurposing into fuel. Leftover charred carbon can be repurposed into another form of bioplastic, which the company even used to 3D print an electric guitar, called the “Trashcaster.”
More options
“I’m not saying it’s a save-the-world type of moment,” Ulven said. “But the more options we have for controlling our discarded waste, the more options we create for sustainability.”
Selling an everyday product made of sustainable materials was the goal of siblings Heather and John McDougall, of St. Paul, Minn.-based Bogobrush. For children of a dentist, the toothbrush seemed to be a perfect product, Heather McDougall said.
But their foray into bamboo toothbrushes was a failure. The wood splintered when drilled for brushes, and slow-drying bamboo warped and attracted mold.
Now the company sells biodegradable and recyclable plant-based plastic toothbrushes made from hemp, as well as cotton, coffee and flax.
A brother, John McDougall, designed the toothbrush, which needed to be tweaked for the tensile and stress properties of hemp-based plastic.
“There’s actually a lot of stress put on a toothbrush handle,” Heather McDougall said.
The toothbrushes are sold online, as well as to luxury resorts such as the Hard Rock Hotel Maldives, which sought ways to counter the company’ single-use plastic footprint, she said.
The company’s U.S. manufacturing partners are learning how to work with different types of bioplastic products in the injection-molding process, giving them more expertise.
“Plastics have done a lot of great things in the world, like being used in airplanes or medical devices,” Heather McDougall said. “But we want to be investing in plant-based plastics that can serve us into the future.”